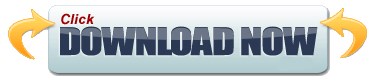

ĭue to complexity of laminated composites, prediction of fatigue behavior in these materials is not straight forward. This is due to lower energy that is required for the initiation of mode I delamination. However, mode I delamination is the most common mode of failure occurred in the structures.

Delamination occurs under different loading conditions, i.e. This failure results in dramatic reduction of residual strength and stiffness of the structure. The principal mode of failure in laminated composites is the separation along the interfaces of the layers, viz, delamination. However, these materials suffer from different damage mechanisms, such as matrix cracking, fiber breakage and delamination. The results indicated that the proposed AE-based method has good applicability to evaluate the delamination crack growth under quasi-static and fatigue loading conditions, especially when the crack is embedded within the structure and could not be seen visually.įiber reinforced plastic composites (FRP) have many advantages such as high specific strength, specific stiffness, etc. The predicted crack growth values was were in a good agreement with the visually recorded data during the tests. Using this correlation the delamination crack growth was predicted under both the static and fatigue loading conditions. It was found that there is a 3rd degree polynomial correlation between the crack growth and the cumulative AE energy. By analyzing the mechanical and AE results, an analytical correlation between the AE energy with the released strain energy and the crack growth was established. To this aim, double cantilever beam specimens were subjected to mode I quasi-static and fatigue loading conditions and the generated AE signals were recorded during the tests.

The aim of this study was to investigate the applicability of acoustic emission (AE) technique to evaluate delamination crack in glass/epoxy composite laminates under quasi-static and fatigue loading.
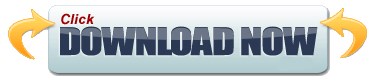